Six Sigma White Belt (CSSC)
- Description
- Curriculum
- FAQ
- Reviews
The Six Sigma White Belt (CSSC) course provides a comprehensive introduction to the Six Sigma methodology, designed for individuals looking to enhance their understanding of process improvement. This course is ideal for professionals seeking to optimize business processes, reduce waste, and improve overall efficiency.
Through this course, learners will delve into the history and development of Six Sigma, exploring its origins and evolution into a crucial business strategy used worldwide. Participants will gain a solid foundation in the basic principles of Six Sigma, learning how to identify and measure process performance using essential Six Sigma tools. The course will cover key concepts such as DMAIC (Define, Measure, Analyze, Improve, Control), enabling learners to understand and apply these methodologies in real-world scenarios.
Additionally, the Six Sigma White Belt course emphasizes the importance of data-driven decision-making, teaching students how to utilize statistical methods to identify root causes of process inefficiencies and make informed improvements. Learners will also explore the roles and responsibilities within a Six Sigma team, understanding how each certification level, from White Belt to Master Black Belt, contributes to successful project outcomes.
This course is tailored for individuals at all levels within an organization, from entry-level employees to senior managers, looking to build a foundational understanding of Six Sigma. Whether you’re new to the field or seeking to reinforce your knowledge, the Six Sigma White Belt course provides the tools and insights needed to drive meaningful process improvements.
Enroll today and take the first step towards mastering Six Sigma methodologies. Enhance your skills, contribute to your organization’s success, and become a valued member of any process improvement team. Subscribe now to start your journey with Six Sigma!
-
1Course IntroVideo lesson
Six Sigma is a methodology for process improvement and a statistical concept that aims to define the variation inherent in any process. The overarching premise is simple: variation in a process leads to opportunities for error, and these errors can result in product defects. By working to reduce variation and opportunities for error, Six Sigma ultimately lowers process costs and increases customer satisfaction. A question you might be wondering about is: What makes Six Sigma so effective and crucial in today's business environments?
-
2Better LearningVideo lesson
To enhance your online learning experience for certification, you need to adopt a structured approach. This includes setting clear, achievable goals and creating a well-defined study schedule. Imagine you are aiming to complete one module per week. By setting this specific target, you create a roadmap that guides your learning journey, helping you stay focused and organized. It's not just about having goals, but about making them actionable and time-bound. This way, you can track your progress and make necessary adjustments to stay on course.
-
3What is Six Sigma?Video lesson
Six Sigma is both a methodology for process improvement and a statistical concept that seeks to define the variation inherent in any process. The core idea of Six Sigma is that variation in a process leads to opportunities for error, and these errors lead to risks of product defects. These defects, whether in a tangible product or a service, result in poor customer satisfaction. By working to reduce variation and opportunities for error, Six Sigma ultimately reduces process costs and increases customer satisfaction. This systematic approach ensures a higher level of quality and efficiency in all organizational processes.
-
4Course Choice, Skill Development and Prior KnowledgeText lesson
-
5Defining 6σVideo lesson
Six Sigma represents a statistical measure that signifies near perfection in a process. To understand it in practical terms, Six Sigma means having only 3.4 defects per million opportunities. This level of precision translates to a staggering 99.99966 percent accuracy. For many businesses, reaching this level of perfection is the ultimate goal, as it ensures an exceptionally high standard of quality and customer satisfaction. But what does a "perfect" process look like? To grasp this concept, let's delve into some real-world examples that highlight the significant impact of Six Sigma on different industries.
-
6Calculating Sigma LevelVideo lesson
Calculating the Sigma Level of a product or process involves understanding a few key concepts and applying a straightforward formula. Let's start by breaking down the basic formula used for this calculation. Yield is calculated by subtracting the number of defects from the number of opportunities, dividing that result by the number of opportunities, and then multiplying by 100. This formula helps to determine how efficiently a process is operating without defects. For instance, if a process has 1,000 opportunities and 50 defects, the yield would be calculated as ((1,000 - 50) / 1,000) * 100, resulting in a yield of 95 percent.
-
7Principles - Customer Focused ImprovementVideo lesson
Six Sigma is a methodology aimed at process improvement and enhancing quality by reducing variability and defects. One of the key principles of Six Sigma is its strong focus on the customer. This focus is not just about increasing the sigma level but about truly understanding and meeting customer needs. How can focusing on the customer improve business processes and outcomes? The answer lies in the detailed understanding and application of customer feedback to tailor processes and products to better serve their needs.
-
8Principles - Continuous Process ImprovementVideo lesson
Continuous process improvement is a cornerstone of the Six Sigma methodology. It is the belief that there is always room for enhancement, no matter how small, in every process within an organization. By continually seeking ways to improve, an organization ensures it is always moving towards higher efficiency and quality. The Six Sigma approach demands a mindset of perpetual growth and development, which means that once an improvement is made in one area, the focus shifts to another. This constant cycle of assessment and enhancement ensures that the organization never settles for "good enough" but always strives for excellence.
-
9Principles - VariationVideo lesson
Variation is an inherent part of any process. Every time something is done, whether it is answering a call or making a pizza, there will be slight differences in the outcome. These differences, known as variation, can impact the quality and consistency of products and services. For example, in a call center with twenty employees, you will find that each phone call is slightly different, even if everyone is following the same script. Factors like inflection, accents, environmental noise, and the mood of both the caller and the employee contribute to this variation. By recognizing and understanding these variations, businesses can start to take steps to minimize them and improve consistency.
-
10Principles - Removing WasteVideo lesson
Removing waste from processes is crucial to improving efficiency and achieving better results. In the context of Six Sigma, waste refers to any item, action, or person that does not add value to the final product or outcome. Think about the hotdog example. Do four different people need to place the hotdog in the bun, add ketchup, plate the hotdog, and then serve it? If this process requires four individuals, it is likely creating unnecessary delays and inefficiencies. By examining such scenarios, I can identify where waste is occurring and find ways to streamline the process.
-
11Principles - Equipping PeopleVideo lesson
In organizations, implementing improved processes is crucial for achieving efficiency and effectiveness. However, simply putting these improvements in place is not enough. It is essential to ensure that employees are equipped to monitor and maintain these improvements for long-term success. Process improvement is not just a one-time event; it is a continuous journey. By understanding and applying the principles of process improvement, organizations can sustain their gains and drive further growth.
-
12Sigma Level Is Not a Final IndicatorVideo lesson
Sigma levels provide a high-level look at how a process is performing, indicating the number of defects per million opportunities. A higher Sigma level means fewer defects and better performance. However, simply comparing Sigma levels between multiple processes does not always point to the particular process an organization should improve first. One must consider costs, resources, and the estimated impact of improvements. For instance, if two processes have similar Sigma levels, but one process impacts customer satisfaction more significantly, the organization might prioritize improving that process.
-
13Principles - Controlling the ProcessVideo lesson
In Six Sigma, controlling the process is fundamental to achieving consistent quality and continuous improvement. An out-of-control process can lead to unpredictable results, increased waste, and dissatisfied customers. It is crucial to bring such processes back into a state of statistical control, ensuring they meet specific performance standards. Once control is established, ongoing monitoring and adjustments keep the process stable. Think of a manufacturing line where variations in temperature or machine speed can affect product quality. By implementing Six Sigma principles, you can identify these issues, correct them, and maintain control to produce high-quality outcomes consistently.
-
14Challenges of Six SigmaVideo lesson
Six Sigma is not without its own challenges. As a comprehensive method that demands a strong commitment to continuous improvement, it is often seen as an expensive or unnecessary process, especially by small or mid-sized organizations. Leadership at Ideal Aerosmith, a manufacturing and engineering company in Minnesota, initially shared this skeptical view. They were concerned about the costs associated with implementing Six Sigma and whether it would be worth the investment. This skepticism is common and often acts as a significant barrier to adopting Six Sigma practices.
-
15Challenges - Lack of SupportVideo lesson
Six Sigma requires support and buy-in at all levels of an organization. Leaders and executives must be willing to back initiatives with resources, both financial and labor-related. Subject-matter experts must be open to sharing information about their processes with project teams, and employees at all levels must embrace the idea of change and improvement and participate in training. Without this broad support, Six Sigma projects can struggle to get off the ground, let alone succeed. The absence of support can manifest in various ways, creating significant barriers to progress.
-
16Challenges - Lack of Resources or KnowledgeVideo lesson
Six Sigma is a powerful methodology for improving business processes, but one of the most significant challenges you might face is the lack of resources. Resources in this context refer not only to financial capital but also to the necessary personnel, tools, and time required to effectively implement Six Sigma projects. Smaller businesses often find it difficult to allocate these resources, as they have tighter budgets and fewer staff members to dedicate to continuous process improvement. However, it is important to remember that while the lack of resources can be a hurdle, it does not have to be a complete barrier to achieving success with Six Sigma.
-
17Challenges - Poor Project ExecutionVideo lesson
Six Sigma is a powerful methodology for improving business processes, but it is not without its challenges. One of the significant hurdles companies face is poor project execution, especially when they are new to Six Sigma. This can be particularly problematic if the first project does not deliver impressive results. Imagine a scenario where the initial project falls flat – this can lead to skepticism about the entire methodology, making it harder to gain support for future projects. It is crucial to understand that the first project needs to be a home run to convince leadership and others who might be on the fence about Six Sigma's potential benefits.
-
18Challenges - Data Access IssuesVideo lesson
Accessing consistent and accurate data streams is critical for making informed decisions in any organization. One of the most common challenges is discovering that an important process metric is not being captured. Imagine running a factory where you believe you are monitoring all crucial aspects, only to find out that machine downtime, a key indicator of efficiency, is not tracked. This missing metric can lead to uninformed decisions, causing delays and increased costs. Addressing this issue requires a thorough review of all processes to ensure that every vital metric is identified and captured accurately from the start.
-
19Six Sigma White Belt (CSSC)Quiz
Understand the basic principles of Six Sigma and its importance in process improvement. Learn how to define and measure process performance using Six Sigma tools.
-
20Six Sigma History and ApplicationVideo lesson
Quality and improvement in business have always been vital for success. Traditional quality programs and continuous process improvement methods are both aimed at enhancing performance and achieving organizational goals. Traditional quality programs, such as Total Quality Management, focus on specific objectives like reducing errors, improving customer satisfaction, and boosting profits. These programs can either run indefinitely, continually striving towards the same goal, or they reach their objective and must be reset for a new target. In contrast, continuous process improvement methods, such as Six Sigma, aim to create a culture of perpetual enhancement, where performance is continuously optimized from within the organization.
-
21The Development of Statistical Process ControlVideo lesson
Six Sigma applies statistics to define, measure, analyze, verify, and control processes. This methodology uses DMAIC and DMADV to accomplish improvements and develop controls for processes. DMAIC stands for Define, Measure, Analyze, Improve, and Control, which are the five phases of a Six Sigma project to improve an existing process. On the other hand, DMADV stands for Define, Measure, Analyze, Design, and Verify, used for developing new processes. Understanding these methodologies is crucial for implementing Six Sigma successfully.
-
22Continuous Process Improvement: Toyota and LeanVideo lesson
In the 1940s and 50s, Toyota faced significant challenges. Japan was recovering from the devastation of World War Two, and the economy needed a boost. Toyota's leadership realized that improving performance and efficiency was crucial for survival and growth. They had explored quality concepts before the war, but the urgency increased post-war. By looking at manufacturing ideas attributed to Henry Ford, Toyota leaders sought to create a system that would enhance production, allow for variable products, reduce costs, and ensure quality. This quest led to the birth of what we now know as the Toyota Production System.
-
23Motorola’s Focus on DefectsVideo lesson
In the mid-1980s, Motorola was facing a significant challenge with the quality of its products. The problem came into sharp focus when a Japanese company took over one of Motorola's television manufacturing plants. The Japanese company's application of Lean concepts resulted in televisions that had only one-twentieth the number of defects compared to those produced by Motorola. This discrepancy raised serious questions about the effectiveness of Motorola's quality management programs and sparked a revolution in the company's approach to quality.
-
24ABB, Allied Signal, and General ElectricVideo lesson
Six Sigma is a methodology that has transformed how businesses operate by emphasizing quality improvement and efficiency. Dr. Harry, a pivotal figure in this field, significantly contributed to the development and evolution of Six Sigma. His journey took an important turn when he left Motorola and joined Asea Brown Boveri. At ABB, he met Richard Schroeder, who would also become a significant advocate for Six Sigma. The collaboration between Dr. Harry and Schroeder led to critical insights that shaped the future of Six Sigma. They realized that, in many ways, business profits could drive quality initiatives. This understanding shifted the focus of Six Sigma from purely quality improvement to a broader business strategy.
-
25Continued Growth of Six SigmaVideo lesson
Six Sigma has grown significantly since its success at General Electric and Motorola. These corporations demonstrated that Six Sigma could lead to substantial improvements in efficiency and cost savings. Following their lead, numerous companies across the country rushed to implement Six Sigma. However, this rush often led to poor execution and a lack of understanding of statistical process control. Some organizations did not take the time to fully grasp the principles of Six Sigma before applying its methods, resulting in disappointing outcomes. Despite these challenges, many companies have achieved remarkable financial benefits through proper implementation of Six Sigma, saving millions, if not billions, of dollars.
-
26Applying Six Sigma Knowledge - The Levels of Six Sigma CertificationVideo lesson
Six Sigma is a highly structured methodology for improving business processes by reducing defects and enhancing quality. It is crucial for organizational success because it provides a systematic approach to identify, analyze, and solve problems, ensuring that processes operate efficiently and effectively. But what is Six Sigma exactly? Six Sigma is a set of techniques and tools for process improvement. It seeks to improve the quality of process outputs by identifying and removing the causes of defects and minimizing variability in manufacturing and business processes. This is achieved through the use of empirical and statistical quality management methods.
-
27Certification ExamsVideo lesson
Certification exams are crucial in the Six Sigma methodology as they ensure that individuals possess the necessary knowledge and skills to apply Six Sigma principles effectively. By passing these exams, you demonstrate your understanding and ability to contribute to continuous improvement initiatives. Certification not only validates your expertise but also enhances your professional credibility and career opportunities. It is essential to grasp the different levels of certification and their specific requirements to prepare adequately.
-
28Six Sigma PrinciplesText lesson
-
29Six Sigma History and ApplicationQuiz
Understand the historical development, key contributors, and fundamental principles of Six Sigma, and learn how to apply Six Sigma methodologies to improve business processes.
-
30Other Process Improvement and Quality MethodsVideo lesson
The history of Six Sigma reveals its close relationship with various other quality-driven initiatives developed over the past century. This connection exists because all successful businesses share a common goal: serving customers with products or services they need while maximizing profit. Understanding this historical context helps to appreciate how Six Sigma has evolved and why it remains relevant. By studying these interconnected methodologies, you gain insights into the underlying principles that drive process improvement and quality management, enabling you to apply these concepts more effectively in your own work.
-
31Lean Process ManagementVideo lesson
Lean Process Management often goes hand-in-hand with Six Sigma principles. Originally developed to reduce waste in a manufacturing environment, Lean principles can be applied to any process involving the movement or creation of goods or services. This includes virtual or digital services, such as computerized workflow processes. Lean focuses on continuous improvements, much like Six Sigma. By providing tools for waste removal, Lean ensures that daily control and improvements can be made to processes. One of these continuous improvement tools is called Kaizen, a Japanese word that translates loosely to "change for the better." The purpose of every change in a Kaizen environment is to eliminate waste and create more value for the customer on a continuous basis.
-
32Total Quality ManagementVideo lesson
Total Quality Management, often referred to as TQM, became a significant buzzword in business circles towards the end of the 20th century. Developed in the 1950s, it took several decades for TQM to gain widespread acceptance in the United States, peaking in popularity during the 1980s. Many executives and business leaders embraced it, sometimes to the point of making it a joke among certain workforces who felt the effort did not always match the results. Remember the story of Jack Welch at General Electric? He was among those who questioned its effectiveness. Despite mixed results, TQM was an essential stepping stone to modern improvement methods like Six Sigma.
-
33Business Process ReengineeringVideo lesson
Business Process Reengineering focuses on making radical changes across an entire organization or process architecture. Unlike Six Sigma, Lean, and Total Quality Management, which aim for continuous incremental improvements, Business Process Reengineering seeks to achieve significant, transformative change. This approach is particularly concerned with the technical processes that run throughout an organization, such as systems, software, data storage, cloud and web processes, and computer-based workflows maintained by human users. Why would an organization choose to undergo Business Process Reengineering, given its potentially high costs and complexity?
-
34Rummler-BracheVideo lesson
Process improvement methods have been evolving since the 1980s, each building on previous ideas to create more effective and efficient systems. Among these methods, Rummler-Brache stands out as a unique approach that integrates elements of Lean and Six Sigma into a cohesive program. Pioneered by Geary Rummler and Alan Brache, this method focuses on improving organizational processes using practical tools. But what makes Rummler-Brache distinct from other process improvement methods? To understand this, let’s delve into its foundational components and the six phases that guide its implementation.
-
35ScrumVideo lesson
Scrum is a project development method that is specifically designed for Agile programming endeavors in technical departments. It is particularly useful when teams want to create new technical products or integrate new developments into existing products within a short timeframe. Scrum projects typically last between two to four weeks, which is considered a very tight timeline for programming projects. This method was developed as programming and development teams needed a way to continuously meet the technical design and improvement needs of other departments without significantly increasing programming or testing hours, or the need to hire additional technical staff. Additionally, Scrum is used to drive faster times to production or market for software and application products.
-
36The Customer Experience Management Method (CEM)Video lesson
The Customer Experience Management Method, or CEM Method, was developed by process improvement consultants to address the needs of organizations outside of manufacturing. This method combines process improvement tools with customer relations management. It was developed in the 1990s by the Virgin Group and gained popularity throughout the 1990s and early 2000s. The focus of CEM is to take an outside-in approach to process improvement, which means looking at what the customer wants or needs and how each process in an organization serves that need.
-
37JumpStartVideo lesson
JumpStart is a unique method within process improvement that focuses on identifying problems and solutions quickly, all within a single session. Unlike other methods that might take a longer time to analyze and verify issues rigorously, JumpStart is fast-paced and designed to spark discussion and quick action. This method is particularly useful when you need to generate ideas and solutions swiftly without getting bogged down in lengthy processes. How can you rapidly identify and solve problems within a single session? The answer lies in the structured yet flexible approach of JumpStart, which we'll explore in detail.
-
38When to Use Six SigmaVideo lesson
Six Sigma is a powerful tool that can be used even when you do not know the cause of a problem. Imagine a situation where your company experiences a sudden drop in profits over several consecutive quarters, and you have no idea why this is happening. You only know that a key metric is not performing as desired. Six Sigma is designed precisely for these scenarios. It allows you to begin a project without needing to know the root cause upfront. By applying its methods, you can start to seek out the causes of the problem, prioritize them, and work toward effective solutions.
-
39Other Process Improvement and Quality MethodsQuiz
To provide familiarity with various quality-driven initiatives, enhancing the ability to integrate Six Sigma concepts with other quality and process improvement methods like Lean, TQM, and Scrum
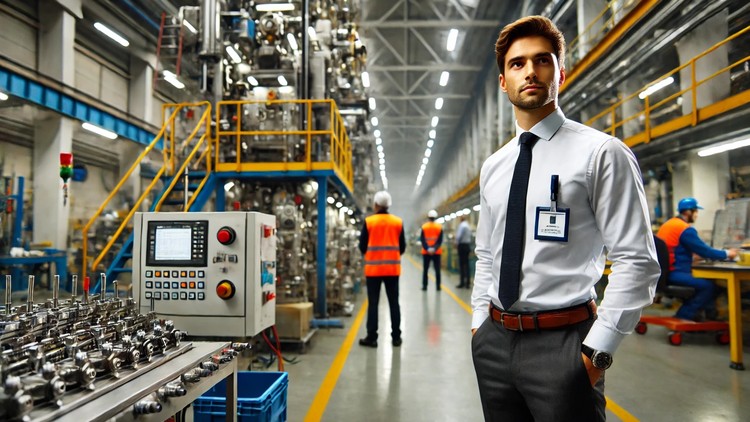
External Links May Contain Affiliate Links read more